We provides you with the latest news on Submersible Dewatering Pump,Dewatering Equipments,Dewatering Pump ,Rainwater Dewatering System,Sludge Dewatering Pump, dewatering on a construction site, dewatering on a construction site,Submersible Dewatering Pump for Construction, Submersible Dewatering Pump for Power plants,Submersible Dewatering Pump for Cements plants,Submersible Dewatering Pump for Thermal plants ,Submersible Dewatering Pump for Shipyard, Dry Dock application,Submersible Dewatering Pumps for Underground Mines ,Submersible Dewatering Pumps for Coal Mines ,Submersible Dewatering Pumps for Coal Mines,Submersible Dewatering Pumps for Open Mines ,Mine dewatering,Submersible Dewatering Pump for Municipal application,
Dewatering
Dewatering is the removal of water from solid material or soil by wet classification, centrifugation, filtration, or similar solid-liquid separation processes, such as removal of residual liquid from a filter cake by a filter press as part of various industrial processes. Construction dewatering, unwatering, or water control are common terms used to describe removal or draining groundwater or surface water from a riverbed, construction site, caisson, or mine shaft, by pumping or evaporation. On a construction site, this dewatering may be implemented before subsurface excavation for foundations, shoring, or cellar space to lower the water table. This frequently involves the use of submersible "dewatering" pumps, centrifugal ("trash") pumps, eductors, or application of vacuum to well points.
Processes
A deep well typically consists of a borehole fitted with a slotted liner and an electric submersible pump. As water is pumped from a deep well, a hydraulic gradient is formed and water flows into the well forming a cone of depression around the well in which there is little or no water remaining in the pore spaces of the surrounding soil. Deep wells work best in soils with a permeability of k = 10−3 m/s to 10−5 m/s; the amount of drawdown that a well can achieve is limited only by the size of the fish pump.
Deep wells can be installed in a ring around an excavation to lower the water level and maintain a safe, dry site. Several equations can be used to design deep well dewatering systems, however many of these are based on empirical data and occasionally fail. Practice and experience, along with a firm understanding of the underlying principles of dewatering, are the best tools for designing a successful system.Some dewatering situations "are so common that they can be designed almost by rule of thumb"
Deep wells are also used for aquifer testing and for groundwater drainage by wells
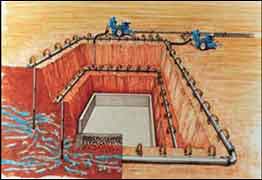
Wellpoints are small-diameter (about 50 mm) tubes with slots near the bottom that are inserted into the ground from which water is drawn by a vacuum generated by a dewatering pump. Wellpoints are typically installed at close centers in a line along or around the edge of an excavation. As a vacuum is limited to 0 bar, the height to which water can be drawn is limited to about 6 meters (in practice) Wellpoints can be installed in stages, with the first reducing the water level by up to five meters, and a second stage, installed at a lower level, lowering it further.The water trickling between the deep wells may be collected by a single row of well point at the toe. This method ensures a much thicker width free from seepage forces
Wellpoint spears are generally used to draw out groundwater in sandy soil conditions and are not as effective in clay or rock conditions. Open pumps are sometimes employed instead of spears if the ground conditions contain significant clay or rock content
The installation of horizontal dewatering systems is relatively easy.A trencher installs an unperforated pipe followed by a synthetic or organic wrapped perforated pipe. The drain length is determined by the drain diameter, soilconditions and the water table. In general drain lengths of 50 meters is common. After installation of the drainpipe a pump is connected to the drain. After the water table has been lowered, the intended construction can start. After the construction is finished the pumps are stopped, and the water table will rise again. Installation depths up to 6 meters are common
Control of pore pressures
Controlling pore pressure is crucial in various engineering and geological contexts, especially in construction, drilling, and geotechnical projects. Pore pressure refers to the pressure exerted by fluids within the pores of a geological formation or a construction material.

Here are some key points related to controlling pore pressure
:1. Importance in Construction and Geotechnical Engineering:
High pore pressures can destabilize slopes, cause landslides, or lead to foundation failures. Controlling pore pressure is essential to ensure the stability and safety of structures.
2. *Methods of Control*:
By draining excess water from the ground or construction site, engineers can lower pore pressures. This can be achieved through pumping, installing drainage systems, or using wells.
Injecting grout or cementitious material into the ground can help stabilize soil and reduce pore pressures.
*Compaction*: By compacting soils or materials during construction, engineers can reduce pore spaces and hence pore pressures.
*Pore Pressure Monitoring*
: Regular monitoring of pore pressures using instruments such as piezometers helps in understanding the dynamics and taking timely preventive measures.
3.*Geological Considerations*
:In geological formations, pore pressure control is critical during drilling operations to prevent blowouts and maintain well stability. Techniques such as mud weight control and casing design are employed to manage pore pressures encountered in subsurface formations.
4.*Environmental Impact*
:Controlling pore pressure also plays a role in environmental management, especially in preventing groundwater contamination and managing fluid migration in geological formations.
Overall, effective control of pore pressure involves a combination of engineering practices, monitoring techniques, and understanding geological conditions to ensure safety, stability, and efficiency in various projects.